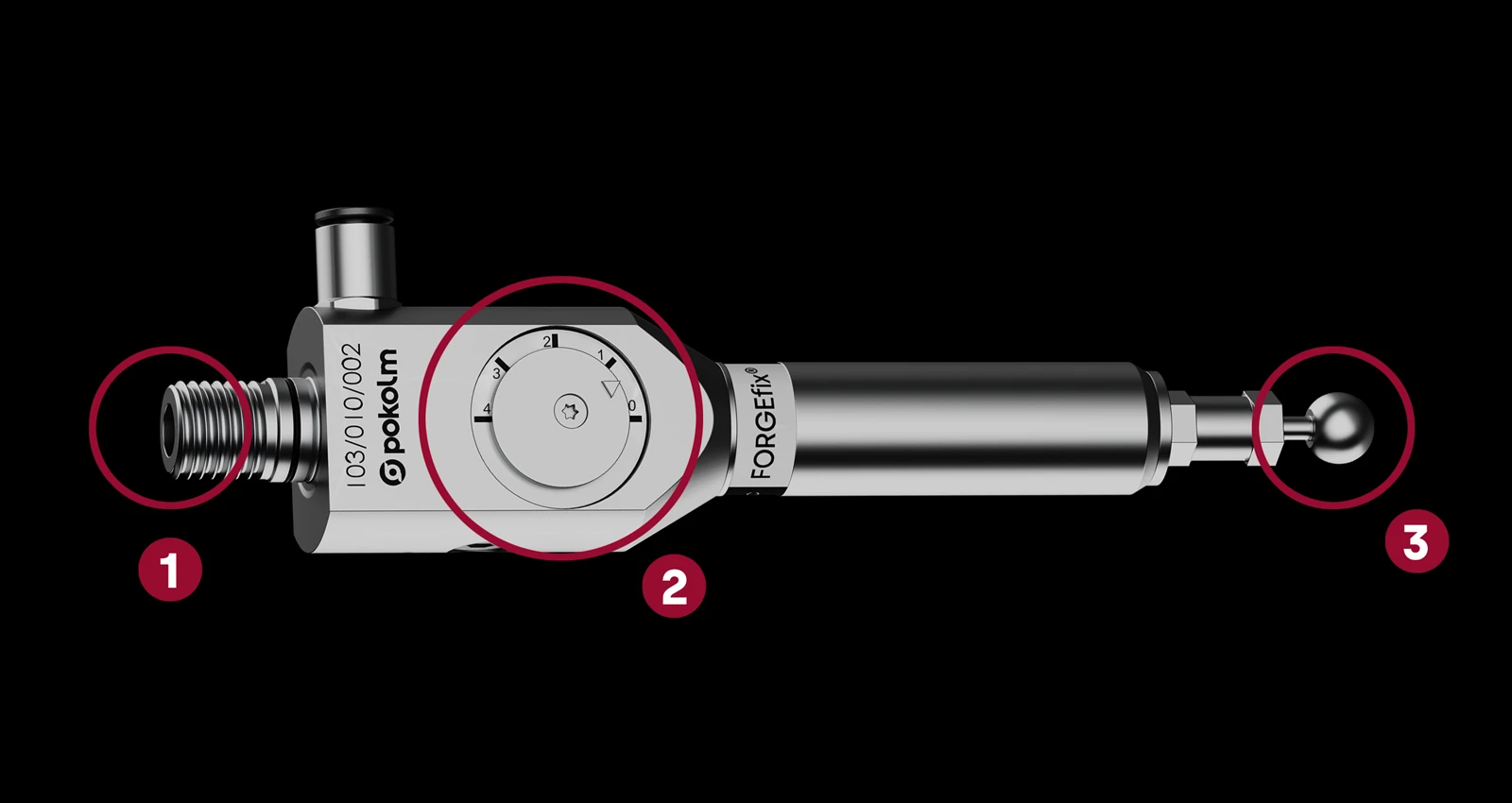
1. Ball Ø 8 mm–20 mm and ram Ø 1 mm–12 mm for all applications and materials 2. Quick adjustment of the impact force: 500 N [SP], 250 N [LP] and 1000 N [HP] 3. Air through the spindle for easy handling in the case of no internal coolant supply; air can be connected externally.