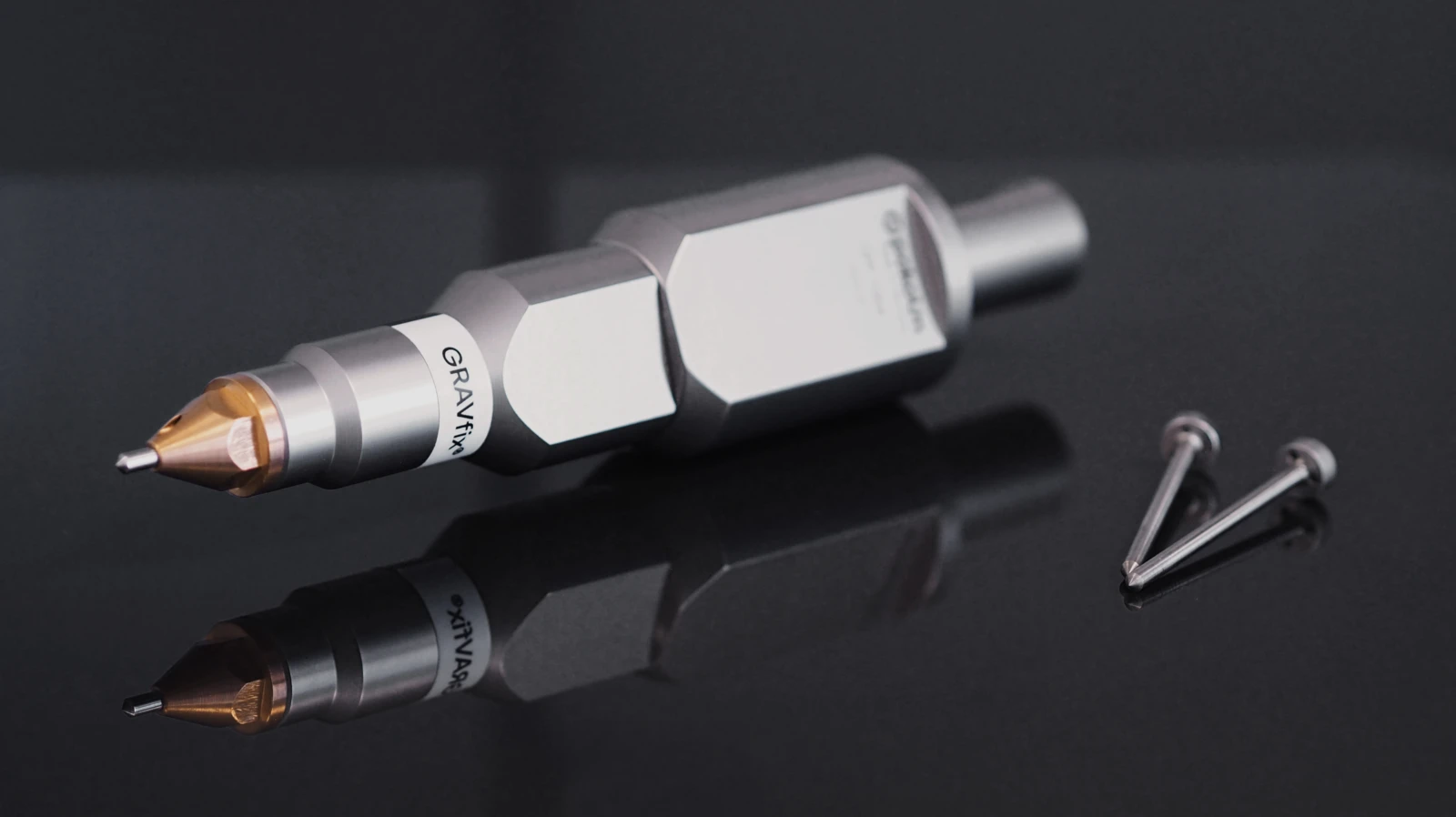
Reliable process chains, maximum precision in production, as well as time and resource efficiency are indispensable success factors not only in the plastics processing industry, but also in many other manufacturing companies.
Reliable process chains, maximum precision in production, as well as time and resource efficiency are indispensable success factors not only in the plastics processing industry, but also in many other manufacturing companies.
At the same time, individualized products are currently very popular with consumers. Many companies are responding to the megatrend of individualization with tailor-made products and small batch sizes.
In order to be able to react quickly to these customer requirements, the development and production of new tools must be designed efficiently. In addition to the rapid implementation of new tools, it is also important to efficiently process changes and adaptations to existing tools.
The eroding machining process offers the possibility of efficiently implementing adaptations and changes to tools. It is a non-cutting manufacturing process in which the workpiece is machined by spark discharge. Material is removed from the surface of the workpiece using electricity until the desired shape is achieved.
In principle, the process can be used to machine any conductive metal such as aluminum, steel, copper, brass or iron. It is particularly suitable for materials that are difficult to machine and whose mechanical processing would lead to rapid wear of conventional tools. This means that hardened steel, hard titanium alloys, carbide, hard materials and conductive high-strength ceramics, which are mainly used in the aerospace industry, can also be easily machined.
When solutions are required to ensure efficient production, Pokolm's technical sales team starts with a holistic analysis.
One specific question from the plastics industry was: Is there an alternative to eroding or milling for markings in injection molds that reduces costs and increases productivity?
Electrode production for markings in tools is time-consuming. In addition, the electrodes have to be measured to set up the CNC machine and taken into account in the programming. Both of these factors mean that eroding in tool and mold making is a machining process with high production costs.
If the marking is milled, fine milling tools such as V-milling cutters or ball cutters remove material. Milling is carried out in several passes in order to obtain clean edges. After milling, the surfaces are polished or blasted to remove burrs.
With Gravfix, Pokolm has another premiumtool in its portfolio that can engrave the marking. The pneumatic needle marker was developed for a wide range of applications and engraves even difficult-to-machine materials precisely and at high speed.
The tests with Gravfix on pre-hardened chrome steel (1.2316) with a working hardness of 50 HRC convinced the customer in terms of process reliability, precision, as well as time and resource efficiency. Since then, Gravfix has replaced the eroding or milling of markings for some tools.