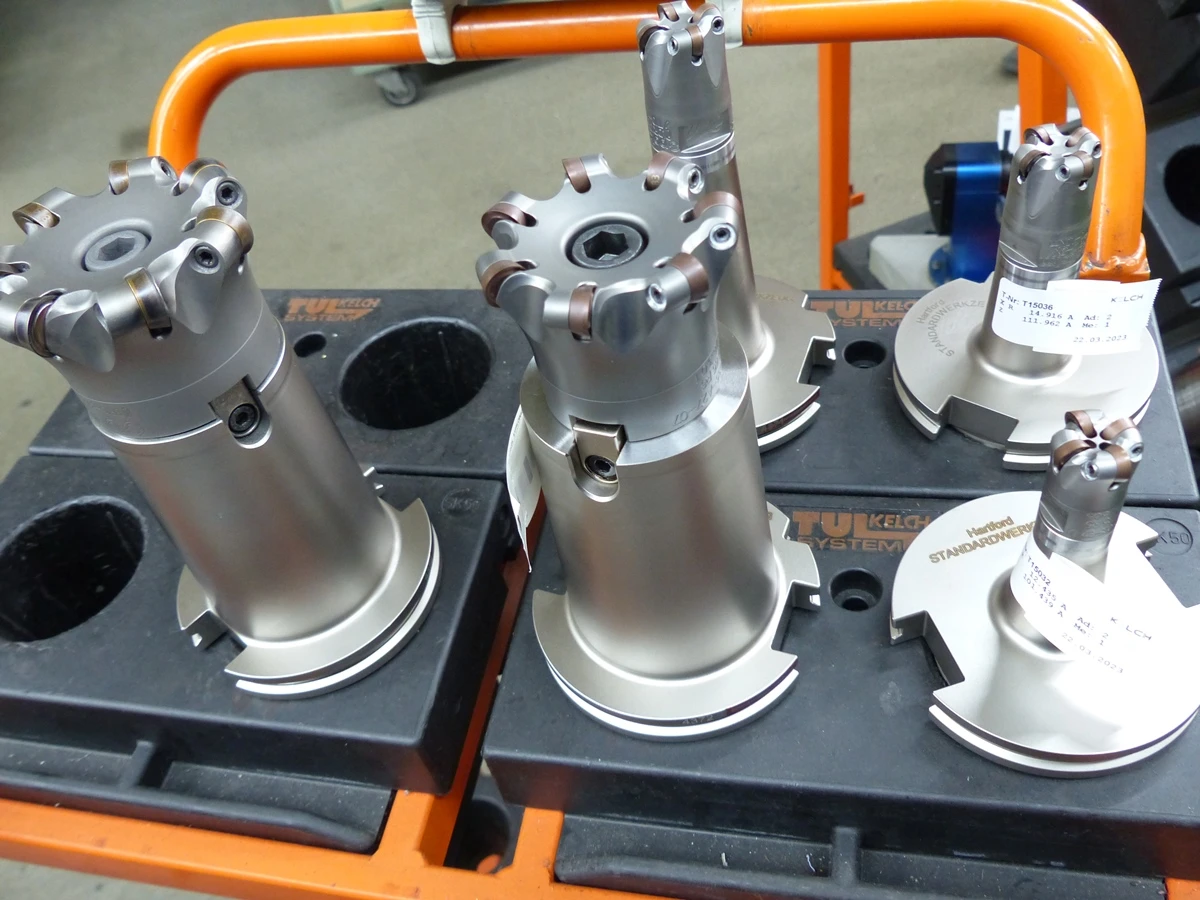
These milling cutters with diameters of 10 to 80 mm are now used for almost all materials because they are seen as having advantages over the stationary insert.
Pokolm’s Spinworx® milling tool with its self-rotating round insert has been on the market for years. Paul Beier GmbH in Kassel was initially just as skeptical about this self-rotating function as many other users. The milling tool has now not only established itself as an extremely versatile solution, it also lets users achieve unprecedented tool life as well as considerable time and cost savings.
Beier’s product portfolio has changed considerably in recent years. The components have become larger and more complex, and the materials the company works with vary greatly. From salts, plastics, hardened steels and stainless steel to stellites and armor steel, Beier does it all. When it comes to roughing these materials, Pokolm’s Spinworx® milling tool with its self-rotating round insert has been the company’s first choice for years.
Matthias Kiehlborn, a cutting machine operator for milling technology at Beier, was a little sceptical at first: “To be honest, I didn’t have high hopes for the self-rotating function, but we tried it and it worked. Over the last four to five years, we have been using the Spinworx® in more and more areas. We now use these milling cutters with diameters of 10 to 80 mm for almost all materials, because we saw clear improvements over the stationary insert. When machining a bearing housing, for instance, we were able to increase tool life by five times by adapting the process.”
These milling cutters with diameters of 10 to 80 mm are now used for almost all materials because they are seen as having advantages over the stationary insert.
Of course, increasing tool life alone is not enough, as Beier also places great importance on process reliability. The company specializes in the production of prototypes, individual parts and small batches of up to 200 units. The advantage of the self-rotating round insert in terms of process reliability is that it is subject to very even wear. This means you can hear it immediately if something is wrong. Thanks to the Spinworx® milling tool, the company was able to switch to multi-machine handling and increase tool life by an average of 30 per cent in the scope of continuous process optimization.
Paul Beier GmbH describes the Spinworx® as a guarantee for long service life which simultaneously reduces the manpower needed to operate the machine. The result: the company was able to introduce multi-machine handling at its site in Kassel.
What’s more impressive is that they did so despite working with some of the most challenging materials out there. Armor steel, for instance, typically has tensile strengths between 1,200 and 1,300 N/mm2, though the company has even worked on steels with 1600 N/mm2. The hardnesses often range between 55 and 65 HRC. However, the hardnesses and strengths of satellite alloys vary enormously. In such critical machining operations, it is not enough to simply adjust your machining strategy. According to Danny Pauer, an application engineer at Pokolm, an intensive dialogue between the tool manufacturer and the user is essential: “The machine operators and programming team at Beier have already visited us in Harsewinkel several times to optimize the way they use our tools. We are familiar with Beier’s product range, which lets us look for tailored solutions. Among other things, this also means that we can develop solutions together depending on the material to be machined and also adapt the inserts to the processes at hand.”
“Another advantage of working with Pokolm is that our new materials are also tested by Pokolm in Harsewinkel. Testing these materials on the machine during operation would be very time-consuming and cost-intensive.”
In addition to minimizing downtime, Beier is of course also concerned with increasing its throughput times. And the Spinworx® is not letting them down. With higher material removal rates thanks to higher cutting speeds and a greater depth of cut, the team was able to drastically reduce production times in some cases. The machining of a forged component is a case in point. For this component, which can have non-uniform hardness with deviations of up to 10 HRC over 100 x 100 mm, the machining time was reduced from four hours to three. However, this time saving is not only due to the higher cutting parameters, it is also due to the fact that the cutting insert no longer needs to be changed. Overall, the reduction in productive and non-productive time leads to freed-up capacity, both in terms of employees and machinery assets.
At Beier, the machining times are just as varied as the materials, ranging from five minutes to ten hours. A classic example here is a component made of armor steel with a tensile strength of 1,300 N/mm2. During machining, 50 kg of chips are produced. However, uninterrupted chip removal is almost inevitable thanks to the rotating cutting insert – and the targeted coolant supply does the rest.
Spinworx®
With all these advantages, one might think that there isn’t anything that Spinworx® can’t do. Danny Pauer doesn’t see it that way, however, because the Spinworx’s strengths primarily come into play in rough machining. Even though the tool is highly versatile, Alexander Dinkel, machining programmer at Beier, can only agree: “We use the Spinworx® exclusively for roughing and, depending on the material, the tool life is between four and twelve hours. The real challenge that we face, though, is the broad spectrum of components and materials that we work on. No standard can help us in that respect. What we need is expert advice. Pokolm provides that, which is why we value the Spinworx® as a flexible tool in our operations.”
We are pleased to see Spinworx® being put to such great use in Kassel. Furthermore, frequent benchmarking in the scope of continuous process optimization measures has so far usually fallen in Pokolm’s favor, with decisive factors including superior service, delivery reliability and open communication when it comes to solving problems.
The company was founded in 1924 as a repair and supply company and was acquired by EVOCO AG in 2021. As a contract manufacturing company and full-service provider, the company specializes in the machining of complex components made from a wide variety of materials. The company has been a Q1 supplier of DB AG since 2005. Another focus of the company is on applications in production systems in the plastics processing industry. The focus here is on the extrusion of thermoplastics as granulates. The company also counts well-known companies from the mechanical engineering, food, defense and supplier industries amongst its customers.
Paul Beier GmbH employs 60 people and is certified in accordance with DIN EN 15085-2, DIN EN ISO 3834-2 and DIN EN ISO 9001:2015.
Left to right: Matthias Kiehlborn, Danny Pauer, Christina Waldeck and Alexander Dinkel