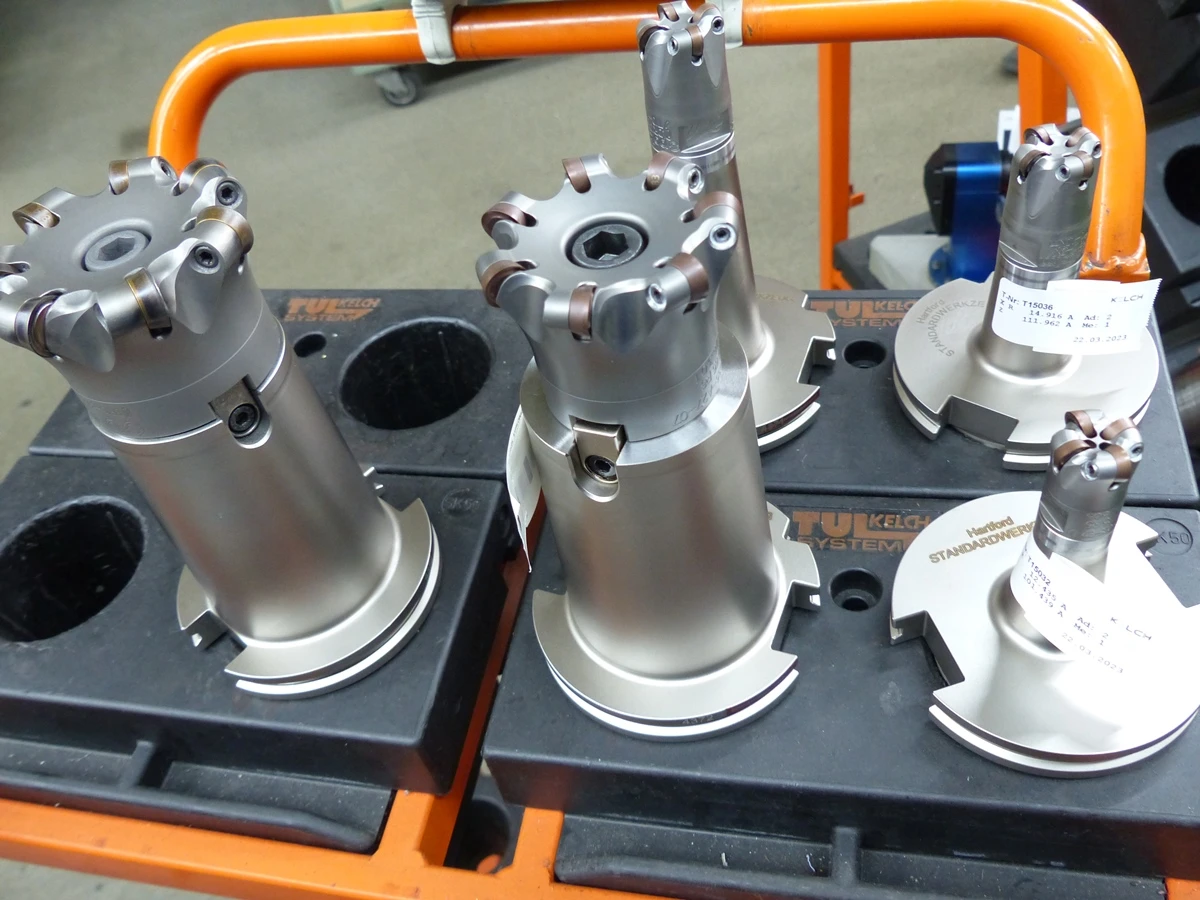
Mittlerweile setzt man diese Fräser mit Durchmesser 10 bis 80 mm bei nahezu allen Werkstoffen ein, weil man gegenüber der stehenden Wendeplatte Vorteile sieht.
Das Fräswerkzeug Spinworx® mit der selbstdrehenden Rundplatte von Pokolm ist seit Jahren auf dem Markt. Die Paul Beier GmbH in Kassel war anfangs bezüglich der Funktion ebenso skeptisch wie zahlreiche anderer Anwender. Mittlerweile setzt man das Fräswerkzeug aber nicht nur enorm vielseitig ein, sondern erreicht nie dagewesene Standzeiten und profitiert von erheblichen Zeit- und Kosteneinsparungen.
Das Produktportfolio hat sich beim Unternehmen Beier in den letzten Jahren stark verändert. Die Bauteile sind größer und komplexer geworden, die zu bearbeitenden Werkstoffe variieren extrem. Von Salzen, Kunststoffen über gehärtete Stähle, Edelstahl bis hin zu Stelliten und Panzerstahl, in Kassel wird nahezu alles bearbeitet. Wenn es um das Schruppen dieser Werkstücke geht, setzt man seit Jahren überwiegend auf das Fräswerkzeug Spinworx®, mit der selbstdrehenden Rundschneidplatte von Pokolm.
Matthias Kiehlborn, Zerspanungsmechaniker Frästechnik bei Beier konnte sich das Anfangs allerdings auch nicht vorstellen: „Um ehrlich zu sein, ich habe nicht an die Funktion geglaubt aber wir haben es probiert und es hat funktioniert. In den letzten vier bis fünf Jahren haben sich bei uns die Einsatzbereiche für den Spinworx® immer mehr vergrößert. Wir setzen diese Fräser mittlerweile mit Durchmesser 10 bis 80 mm bei nahezu allen Werkstoffen ein, weil wir uns damit gegenüber der stehenden Wendeplatte klar verbessert haben. Bei der Bearbeitung eines Lagergehäuses konnten wir damit beispielsweise durch eine Anpassung des Prozesses die Standzeiten um das Fünffache erhöhen.“
Mittlerweile setzt man diese Fräser mit Durchmesser 10 bis 80 mm bei nahezu allen Werkstoffen ein, weil man gegenüber der stehenden Wendeplatte Vorteile sieht.
Allein mit der Erhöhung der Standzeiten ist es natürlich nicht getan, denn beim Unternehmen Beier hat auch die Prozesssicherheit einen hohen Stellenwert. Man konzentriert sich auf die Fertigung von Prototypen, Einzelteilen und Kleinserien bis 200 Stück. Der Vorteil in Sachen Prozesssicherheit der drehenden Rundplatte ist, dass sie sehr gleichmäßig verschleißt. Demnach hört man sofort, wenn etwas nicht stimmt. So konnte man mit dem Einsatz des Fräswerkzeugs Spinworx® auf eine Mehrmaschinenbedienung übergehen und im Rahmen einer kontinuierlichen Prozessoptimierung die Standzeiten im Durchschnitt um 30 Prozent erhöhen.
Bei der Paul Beier GmbH bezeichnet man den Spinworx® als Garant für Standzeiten, der gleichzeitig die Manpower an der Maschine reduziert. Das Ergebnis: In Kassel konnte eine Mehrmaschinenbedienung realisiert werden.
Und das obwohl die Werkstoffeigenschaften in Kassel nicht ohne sind. Die Standards bei Panzerstahl sind Zugfestigkeiten zwischen 1.200 bis 1.300 N/mm2. Teilweise wurden aber auch schon Stähle mit 1600 N/mm2 bearbeitet. Bei den Härten bewegt man sich häufig zwischen 55 und 65 HRC. Bei genannten Stelliten schwanken diese Härten und Festigkeiten allerdings enorm. In solch kritischen Bearbeitungen reicht es nicht, nur die Strategien zu ändern. Vielmehr, so Danny Pauer, Anwendungstechniker bei Pokolm, ist der intensive Austausch zwischen Werkzeughersteller und Anwender notwendig: „Die Zerspanungstechniker und die Programmierung von Beier waren schon mehrmals bei uns in Harsewinkel, um die Werkzeuge optimal einzusetzen. Uns ist die Produktpalette von Beier bekannt und so kann man gezielt nach Lösungen suchen. Dazu gehört u.a. auch, dass wir je nach zu bearbeitendem Material gemeinsam Operationen entwickeln und auch die Schneidplatten an Prozesse anpassen.“
„Ein weiterer Vorteil bei Pokolm ist, dass unsere neuen Werkstoffe auch bei Pokolm in Harsewinkel getestet werden. Diese Werkstoffe bei uns im laufenden Betrieb an der Maschine zu testen wäre ja sehr zeit- und kostenintensiv.“
Neben den Standzeiten geht es in Kassel natürlich auch um Durchlaufzeiten. Und auch hier kann der Spinworx® überzeugen. Mit mehr Spanvolumen durch höhere Schnittgeschwindigkeiten und mehr Zustellung konnten die Fertigungszeiten teilweise drastisch verringert werden. Die Bearbeitung eines geschmiedeten Bauteils macht das deutlich. Bei diesem Bauteil, das auf 100 x 100 mm einen Härteunterschied bis zu 10 HRC aufweisen kann, wurde die Bearbeitung von vier Stunden auf drei reduziert. Diese Einsparung resultiert allerdings nicht nur aus den höheren Schnittdaten, sondern auch aus der Tatsache, dass die Schneidplatte nicht mehr gewechselt werden muss. In der Summe führt die Reduzierung von Haupt- und Nebenzeiten natürlich zu freiwerdenden Kapazitäten. Das gilt für Mitarbeiter und Maschine.
Nun variieren bei Beier nicht nur die Werkstoffe, sondern auch die Bearbeitungszeiten, die zwischen fünf Minuten und zehn Stunden liegen können. Ein klassisches Beispiel ist hier ein Bauteil aus Panzerstahl mit einer Zugfestigkeit von 1.300 N/mm2. Während der Bearbeitung fallen 50 kg Späne an. Durch die drehende Schneidplatte ist die Spanabfuhr aber fast schon zwangsläufig gegeben und die gezielte Kühlmittelzufuhr tut ihr Übriges.
Spinworx®
Durch all diese Vorteile könnte man nun annehmen, dass Spinworx® ein absolutes Allroundwerkzeug ist. Danny Pauer sieht das allerdings nicht so, denn die Stärken des Spinworx kommen vorrangig in der Schruppbearbeitung zum Tragen. Auch wenn das Werkzeug sehr vielfältig einsetzbar ist, kann sich Alexander Dinkel, Programmierung bei Beier, dem nur anschließen: „Wir setzen den Spinworx® ausschließlich zum Schruppen ein und bewegen uns da bei den Standzeiten, je nach Material, zwischen vier und 12 Stunden. Die tatsächliche Herausforderung sind allerdings unsere unterschiedlichen Bauteile und Werkstoffe. Da hilft kein Standard, da brauchen wir fachkundige Beratung. Das ist ja alles gegeben, deshalb sehen wir bei unserem Produktportfolio den Spinworx® durchaus als ein flexibel einsetzbares Werkzeug.“
Wie es scheint, hat man in Kassel mit dem Spinworx® das ideale Werkzeug gefunden. Im Rahmen der ständigen Suche nach Prozessoptimierung hat man allerdings schon häufiger Benchmarks vorgenommen. Das Ergebnis, meist konnte Pokolm überzeugen. Ausschlaggebend dafür war u.a. der Service, die Liefertreue und die offene Kommunikation, wenn es darum geht, Probleme zu lösen.
Das Unternehmen wurde 1924 als Reparatur- und Zulieferbetrieb gegründet und 2021 durch die EVOCO AG übernommen. Als Lohnfertigungsunternehmen und Komplettanbieter konzentriert man sich auf die Bearbeitung komplexer Bauteile aus den unterschiedlichsten Materialen. Seit 2005 ist man Q1-Lieferant der DB AG. Ein weiterer Schwerpunkt sind Anwendungen in Produktionsanlagen der kunststoffverarbeitenden Industrie. Der Fokus liegt hier auf der Extrusion thermoplastischer Kunststoffe als Granulate. Außerdem zählen namhafte Unternehmen aus den Industriezweigen Maschinenbau, Lebensmittelindustrie sowie Defence und Zulieferindustrie zum Kundenkreis.
Die Paul Beier GmbH beschäftigt 60 Mitarbeiter und ist nach DIN EN 15085-2, DIN EN ISO 3834-2 und DIN EN ISO 9001:2015 zertifiziert.
Von links nach rechts: Matthias Kiehlborn, Danny Pauer, Christina Waldeck und Alexander Dinkel